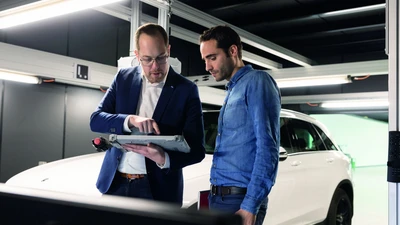
Driverless Safety
The first driverless cars are scheduled to go into production in 2025. Manufacturers will need to ensure early planning for the necessary production systems. Dürr has therefore developed test stands for fully automated testing of self-driving cars.
The new car rolls off the assembly line. Its engine starts automatically. The vehicle drives itself to the final stations in the plant – the end-of-line test stands. It maneuvers into the correct position. Lasers light up, the car is automatically measured, and a large screen then swings into place in front of the hood. The simulated test drive begins shortly after that. Fully automatically. Gas, brakes, sensor systems – state-of-the-art software has completed all the checks within just a few minutes, without any human intervention. The driverless car drives slowly away from the test stand and is ready for shipping to the customer a short time later.
For the moment, this scene only exists in a computer animation, but it could already reflect reality in many automobile plants. Development Director Dr. Thomas Tentrup and his 20-strong project team at Dürr Assembly Products in Püttlingen, in the German state of Saarland, have designed test stands that enable fully automated end-of-line testing of conventional cars – while also offering so much more: “They also permit automated testing of autonomous and semiautonomous vehicles,” says Tentrup.
Manufacturers are already selling cars that can cover short distances driverlessly. Their plan is to launch fully automated cars from 2025 onward. In-plant testing will then become even more crucial because occupants will have to have implicit faith in the faultless operation of self-driving vehicles. Tentrup confirms that the necessary testing technology is already available. “We are prepared for the age of autonomous driving.”
Revolution in the end-of-line area
Final testing before operation
Test stands are some of the most important stations of the automotive production process. This is where the decision is made as to whether a car can be shipped or has to be sent for reworking. All functions that have a bearing on safety are meticulously inspected once more. The results are so important that they are stored in databases. In the event of an accident even years later, manufacturers can then demonstrate that testing was carried out correctly. This documented proof will become even more important with driverless cars.
Car manufacturers around the world rely on test stands from Dürr Assembly Products, which are also manufactured in China, Brazil and the Czech Republic in addition to Germany. Püttlingen is home to the parent plant, where workers manufacture the test stands to customer specification in large production buildings. They assemble metal framework structures, on which they then mount motors and sensor systems. However, a large part of the work takes place in the background rather than on the shop floor itself. Dürr experts develop and design the test stands on the computer and provide them with the appropriate software.
Test stands are not off-the-shelf products. “They consist of modules that are individually combined,” states Tentrup. Exactly what they look like depends primarily on the vehicle manufacturers and the models they have to test. The experts from Püttlingen continuously improve their products. The company has a groundbreaking, patentpending innovation in the form of the → x-road curve test stand, on which autonomous and semiautonomous vehicles can be tested. But it also makes testing of conventional cars substantially simpler.
Berlin buses operate driverlessly
Autonomous driving can already be seen in action in Berlin, where automated buses transport patients and visitors to their destination on the Charité hospital site. The small, yellow vehicles of the BVG, Berlin’s municipal public transport company, travel almost silently along a defined route. They operate across the extensive site with its institutes, restaurant and administrative buildings at a speed of up to twelve kilometers per hour. The pilot project, under the name “Stimulate”, is scheduled to run until 2020 with the aim of providing answers to practical questions on autonomous driving.
Tiltable rollers prevent vehicle drift
Up till now, there has always had to be a person at the wheel to drive a new car onto the test stand. The driver parks the wheels of the drive axle on rollers mounted in the floor of the platform. Pressing the gas pedal causes the wheels and the rollers to rotate. The vehicle therefore remains on the same spot. However, if the steering wheel is not set to drive straight ahead, the vehicle moves to one side or the other. Someone therefore has to correct the steering to prevent the car from breaking away laterally. With the new x-road curve test stand, that is no longer necessary. Design engineer Stefan Rothfuchs points to two tiltable roller mounts. They automatically correct steering movements by the wheels. Two lines of red light shimmer on the sidewalls of the tires. “Laser sensors measure the wheel angle relative to the roller mounts,” explains Rothfuchs. Smart software analyzes the data and transmits control signals to electric motors that adjust the direction of the rollers. In this way, they correct the wheels’ steering movements and prevent the vehicle from drifting to the side. Tests can therefore be run automatically without having to have a driver at the wheel to intervene. In addition, cornering can also be simulated in a practical test for the first time.
Although the principle sounds simple, the development of the tiltable rollers was difficult. According to Tentrup, who has a doctorate in theoretical physics, understanding the force that acts when the wheels make a steering movement was one of the major challenges. “It took us a long time to understand the effect.” Since there was nothing in the literature either, the principles had to be developed in-house with support from universities, and verified in a computer model. Only once the developers had grasped the principle did they move on to designing the new test stand. Today, Dürr also supplies the tiltable roller units as a retrofit kit that vehicle manufacturers can use to upgrade existing test stands.
Virtual streets and scenery
The x-road curve can be linked to virtual scenery that passes by on a screen to test autonomous vehicles. That means the car drives along the road as in a computer game and tackles various traffic situations. This enables the system to test how well the electronic systems work in conjunction with autonomous or semiautonomous driving. Do they detect obstacles quickly enough? Do they register traffic lights, traffic signs and avenues of trees? Are pedestrians identified in good time in the dark? Driver assistance systems, as fitted in practically all new cars, already handle some of these tasks. They are more or less the precursors of autonomous driving, operating by means of a camera, laser or radar.
A handful of these sensors are tested in passing on conventional test stands. But their number rises every time a model is changed. “We assume that around 40 sensors will have to be calibrated in autonomous vehicles,” says Tentrup. This high number would exceed the capabilities of conventional test stands. Particularly as the sensors in a driverless car have to work with extreme precision. They will play a crucial role in safe driving with autonomous vehicles.
Lights out
Calibration of the safety-relevant sensors is therefore a crucial step – for which Dürr has developed the new → x-around test stand. It looks like a garage and can be completely blacked out. That is important as no interference from a light source can be permitted while the sensors of an autonomous car are finding their optimal position.
The chassis geometry of each vehicle must be precisely measured before the sensors are calibrated on the test stand. Every vehicle deviates from the specifications as a result of production tolerances. These variations have to be taken into account during setup so that the sensors can precisely determine distances from objects and their speeds.
Our test stands consist of modules that are individually combined.
Dr. Thomas Tentrup , Development Director
Martin Wagner, Product Manager Autonomous Driving, shows how the sensors are set up. A screen swings into place in front of the vehicle, and it goes dark in the test stand. Patterns of circles and rectangles are displayed on the monitor, similar to an eye test. “The optical sensors are automatically calibrated with the aid of the outlines,” explains Wagner. Test stands often still use printed panels to calibrate the sensors, but the Püttlingen developers regard that as unsatisfactory. “We have found that the most precise results are achieved when the calibration patterns are displayed on monitors,” says Development Director Tentrup.
Setup takes just a few minutes. The vehicle can then exit the test stand. Tentrup is happy. Dürr unveiled the new test stands to car manufacturers from around the world in the fall of 2018. The first sales talks are underway – which indicates that fully automated testing in automotive plants will become standard before the first autonomous vehicles roll off the production line.