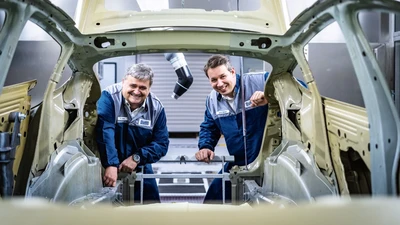
Pit stop
Mar 18, 2021
Rigid conveyor belts? Fixed cycle times? In the paint shop of the future, both will now be a thing of the past. Dürr’s new concept relies on flexible painting boxes and automated guided vehicles, which are used to move the car bodies freely through the factory building. This also dispenses with the need for preset cycle times.
EcoProFleet
The automated guided vehicle system replaces the conveyor technology of traditional painting lines.
There is dense traffic in the paint shop of the future. → Automated guided vehicles (AGVs) continuously move car bodies from the high-bay warehouse to the working boxes located next to the transit routes. Shortly after the AGVs have dropped off their cargo, the robots begin the painting process. As soon as all paint coats have been applied and dried, a vehicle transports the colored car bodies onward. A digital manufacturing execution system controls the processes in the background.
This is what the paint shops of the automotive world could soon look like. For Frank Herre, it is only a question of time before this flexible concept replaces the rigid painting line. As much as 15 years ago, the head of application development at Dürr was wondering how the increasingly broad range of OEM vehicles might be painted even more efficiently. He sketched the first drawings on a napkin in a café in Tokyo while on a business trip. This was followed by many years of development work in cross-divisional teams. The result was the new concept for the → paint shop of the future. “It’s a revolution,” says Herre.
A break from tradition
DXQ Control
Thanks to smart software, production can be controlled more efficiently – an important task in the paint shop of the future.
Manufacturers are showing great interest since conventional in-line paint application is being pushed to its limits in meeting current demands. Using the conveyor belt principle, it involves car bodies being processed one after the other. Every work stage takes the same amount of time. “This kind of system is perfect when the painting line is used for producing a single model,” says Jens Reiner, Research and Development Director for Paint Shops at Dürr.
But this is hardly ever the case nowadays. The variety of models is growing and manufacturers are building their plants in close proximity to the customer in order to save transport costs and customs duties.
This is why, in an ideal case, they need factories in which the entire range of models can roll off the production line – from the smallest car through to the SUV.
Small car bodies can be painted more quickly. “But it’s the large car bodies that determine the duration of a work stage, although they often only make up 20 percent of total production,” says Reiner. In the flexible paint shop of the future, this will no longer be the case. Just like in a car wash with self-service wash bays, every work stage only takes as long as necessary. As soon as a station becomes available, it is occupied by a new car body. This increases efficiency.
Boxes as a central component
The key component of this concept is the newly developed → EcoProBooth painting box. It is as large as two overseas shipping containers and works both flexibly and extremely quickly. In it, up to eight robots paint the interior and exterior of the car body. Until now, this has required two or sometimes three separate booths along the painting line, which means up to 30 seconds of transport time. That is now a thing of the past. It may not seem much but, with huge production volumes often exceeding 200,000 vehicles per year, it all adds up: The time saved is equivalent to that of several thousand painting processes.
More time can be saved if boxes specialize in a single color such as white, which is ordered for every third vehicle worldwide.
EcoProBooth & Painting Robots
The new painting box is around 60 qm in size. This is where the robots (up to 8) paint the interior and exterior of car bodies – in conventional painting lines, several stations are needed for this job. The customer can equip it for certain types of painting work – such as the application of popular colors or decorative and contrasting colors.
This dispenses with the need for colors to be changed and the paint atomizer to be cleaned which, in turn, saves time. The lower costs of materials also make a difference. Per factory, the cost benefit achieved through this alone could be around half a million euros per year, according to Herre’s calculations. Due to the lower energy consumption and solvent use, the environmental impact is reduced as well. This is important for automakers, since they have set themselves the goal of becoming climate-neutral.
To increase efficiency further, it would also be possible to install boxes in which robots paint car bodies in rare colors or provide them with decorative stripes. These work stages are partly carried out manually and are currently very time-consuming.
Benefits for new entrants
Maintenance windows
Atomizers fitted to the robots can be cleaned and serviced quickly and without any respiratory protection through the four maintenance windows of the painting box.
The box concept offers even more advantages to those manufacturers who do not know how many vehicles they will be producing in the coming years. It is above all new electric vehicle manufacturers who find themselves in this position. “They can install more boxes straightaway, if required,” says Jens Reiner. Rigid painting lines do not allow for the production capacity to be expanded that easily: Every modification involves a production standstill lasting several weeks – provided there is enough space.
The reverse is also possible: When their facilities are not fully utilized, the box concept gives manufacturers a high level of flexibility. “They can then leave one or several stations idle,” says Reiner.
This lowers operating costs. As soon as the number of orders increases again, production can be ramped up quickly.
Another key element in the paint shop of the future are the → automated guided vehicles that transport the car bodies. A Dürr team has developed these vehicles itself. “There is no vehicle on the market that meets our requirements,” explains Reiner. All existing models must go to a station each night to recharge their energy stores. This means they cannot operate around the clock. Dürr’s vehicles, however, regularly connect to charging stations during their 24/7 operation. These stations are situated along their routes, at places where the vehicle stops anyway, for example at an unloading point.
THE PAINT SHOP AS A LAB OF THE FUTURE
The → paint shop of the future is like a toolbox with space for further solutions on which Dürr experts work across different divisions. Maintenance windows in the painting boxes are one example. “They make it easier to clean or service the paint atomizer fitted to the robots,” says developer Herre. In the conventional paint application concept, the line has to be stopped to do that. A worker wearing respiratory protection enters the booth, perhaps bringing in contaminants that land on a freshly painted car body.
From now on, the respective robot will be the only one interrupting its work to reach its arm through one of the four windows into a small maintenance cell. From this well-ventilated cell, the atomizer can be cleaned or repaired without any respiratory protection. Paint shop expert Reiner is convinced: “Be it paint application, conveyor technology, sealing or exhaust-air purification – more innovations will soon follow.” The interdisciplinary development teams are working hard to also develop new software applications. These will make operations even more efficient. After all, Dürr’s paint shops are to remain ahead of their time, well into the future.
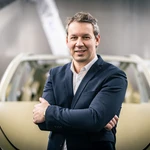
Jens
Reiner
Senior Vice President
Sales
Dürr Systems AG
Carl-Benz-Str. 34
74321 Bietigheim-Bissingen
Germany
Carl-Benz-Str. 34
74321 Bietigheim-Bissingen
Germany