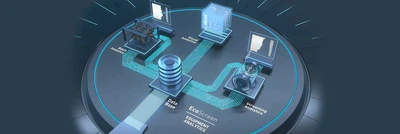
Smart paint shops with DXQequipment.analytics
Mar 4, 2019
Continuous recording, analysis and evaluation of process data with Dürr’s digital innovation
Developed by Dürr, the DXQequipment.analytics (formerly EcoScreen Equipment Analytics) software records, evaluates and visualizes robot and process data. It is designed to make processes more efficient, eliminate faults, support maintenance work and ensure product quality. The technological highlight is a Streaming Analytics application for real-time data analysis.
The software seamlessly records all data from the painting process and analyzes it. Based on this, a ‘digital fingerprint’ is created for each painted car body. It contains information, for example, on the robots’ movements, on paint consumption, and on the exact position of the car body during painting. If a quality problem occurs, the cause can be determined immediately using the recorded data. The plant operator can perform analyses for any painted car by projecting the path taken by the painting robot onto the CAD model of the car body on the screen.
Alogarithms calculate the ideal plant condition
The Streaming Analytics function of → DXQequipment.analytics is used, for example, for online quality control during the painting of cars. Here, algorithms analyze data – such as paint flow – from the painting process in real time and show anomalies. This enables the operator to react immediately, thus preventing further car bodies from being painted incorrectly. The algorithms can easily be created by means of a graphic user interface – without any programming knowledge.

230
evaluable signals
per robot

2,000,000 kB
of data per robot
per day

Endless
opportunities for
process monitoring

100%
transparency of the
production process
The Streaming Analytics application is already being used in the paint shop of a German automaker. It is based on a software module from the ADAMOS IIoT platform. Dürr is currently working on the integration of a Batch Analytics function in → DXQequipment.analytics. Here, the software analyzes historical data, detects trends, and uses artificial intelligence to develop predictions and recommended actions.
The DXQequipment.analytics software offers customers new possibilities for quality assurance and for process analysis in paint shops. In addition to the ADAMOS IIoT platform, it forms another milestone in the digitization of production processes.
"Our digital innovations are turning paint shops into smart factories", says Ralf W. Dieter, CEO of Dürr AG. "DXQequipment.analytics includes both current software technologies and Dürr’s special expertise in the painting process. This is how we are offering efficient solutions for the smart networking of the painting process."
Our digital innovations are turning paint shops into smart factories.
Ralf W. Dieter, CEO of Dürr AG
Dürr's Digital Factory
The → DXQequipment.analytics software was developed in the Dürr Digital Factory. Founded at the beginning of 2018, this competence center has around 100 software experts working on solutions for the digitization of production processes.
Find out more about how the → digital@DÜRR strategy enables Dürr to prepare itself for Industry 4.0.