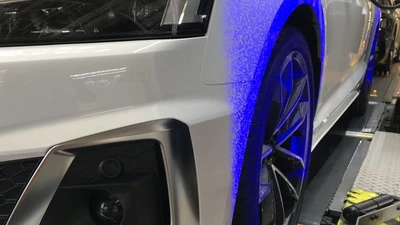
Greater flexibility in the measuring and testing area
Mar 10, 2021
x-3Dsurface: new sensor from Dürr Assembly Products successfully positioned on the market
The large number of differing body shapes and tire sizes that vary within one production line require an ever-increasing degree of flexibility in the end-of-line measuring and testing area. With this in mind, the testing specialists from Dürr Assembly Products developed the flexible x-3Dsurface sensor for chassis geometry measurement. Multiple customer projects provide impressive proof that the new sensor has been positioned on the market successfully.
Its outstanding properties are that it is ready to perform measurements immediately and its highly precise area-based measurement. It contains considerably more information than the previous line-based measurement. These strengths allow the customer to perform an efficient and stable chassis geometry measurement. Furthermore, → x-3Dsurface distinguishes itself by being easy to integrate into existing systems and enabling height measurement without additional lighting.
The two cameras of this contact-free system capture the entire lateral surface of the wheel and the edge of the wheel arch and display it as a three-dimensional “measuring surface in space”. This measuring surface is used to calculate the chassis geometry and body height at the edge of the wheel arch. Precise adjustment of the chassis geometry ensures that the steering wheel remains straight while the vehicle is driving straight ahead and also ensures optimized tire wear.
AUDI AG produces differing models on a number of assembly lines in Ingolstadt. Each of these lines is equipped with wheel alignment stands from Dürr. Following joint tests with Audi that took place at the plant of a Dürr subsidiary in Püttlingen (Germany), the first wheel alignment stand was modified with x-3Dsurface. On this pilot system, the testing specialists verified the accuracy, function, and availability of the system on the master gauge, the rolling master, and various vehicle types. More than 200 tests were conducted together with the customer.
Based on these test results, Dürr received the approval to launch the new system in production. The first modified test stand has been running successfully on the assembly line since February 2020.
Quick to integrate and ready for use
The modification revealed one of the sensor’s advantages: It is easy to integrate in the existing wheel alignment stands x-wheel from Dürr.
Audi was so impressed with the new technology that two further wheel alignment stands were modified with x-3Dsurface in the summer of 2020. The other four wheel alignment stands on the assembly lines in Ingolstadt will be modified over the coming months.
At SEAT Martorell in Spain, Dürr modified two test stands of the single-line measuring system x-contour to x-3Dsurface over Christmas. The reason for carrying out this project is the greater mix of vehicles and the more difficult conditions in the context of integrating small vehicles and large CUVs (crossover utility vehicles) resulting from this.
At VW Zwickau, the first test stand was converted to x-3Dsurface in January. The preceding model from Dürr, the → x-3Dprofile, had been in use there previously.
More precise measurement
Compared to the predecessor, the measured area of x-3Dsurface contains considerably more information. This yields a more stable and precise measurement.
The sensor has even convinced customers outside of Europe. Four new wheel alignment stands are being equipped with x-3Dsurface at FAW Hongqi. This is the first order for the sensor in China.
Premieres in the truck field
The sensor is also excellently suited for the end-of-line area in truck production, as demonstrated by two projects at premium truck manufacturers in Europe. The first test stand with the new sensor in this market segment serves to expand capacity. A further x-wheel truck d system including x-3Dsurface will be added to existing production in the course of 2021.
There is another premiere at a different manufacturer, where the new x-wheel truck d for calibrating the radar of the driver assistance systems is even equipped with four instead of two x-3Dsurface sensors for the first time.
Efficient final assembly of the future: NEXT.assembly from Dürr
Dürr has bundled its technological expertise for the efficient final assembly of the future under the name “NEXT.assembly.” With its products and solutions for end-of-line testing technology, Dürr Assembly Products constitutes one pillar in this endeavor.
NEXT.assembly is the most extensive offer on the market: From planning and consulting to the implementation of individual processes in conveyor, gluing, marriage, filling and testing technology to process-optimized complete plants (“one-stop-shop”).
Dürr uses synergies at all levels and achieves increased added value for its customers not least through intelligent and connected processes.