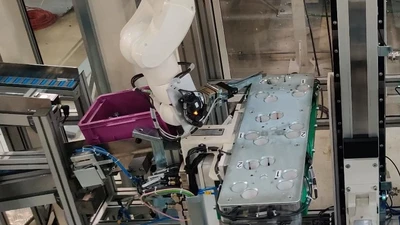
Helper with a sharp eye
Oct 8, 2021
Automatic x-elect bolt picking system
Pioneering new development for assembly: Dürr’s x-elect is an automatic bolt picking system for direct bolting. The BMW Group is the first customer to use the bolt picking system at its Leipzig plant, namely in the marriage line when bolting the high-voltage batteries.
x-elect contains a software-controlled robot that picks up the bolts using a gripper, without the need for manual intervention. The key component here is a 3D camera system, which identifies the right parts in the container. x-elect can use a variety of different bolts: M8 to M16, various head designs, up to 130 mm length.
In the first customer project at the BMW Group plant in Leipzig, two bolt picking systems have completed their practical test with flying colors. Since mid-July, the first pre-series vehicles have been passing through the bolting station, in which six Dürr x-gun bolting systems are supported by two x-elect systems. In the bolt picking system, the robot places the right parts into the bolt nests. The loaded nests move up to the loading position of the x-gun. The direct nutrunners, which have been established in the market for years, then perform up to four bolting operations, one after the other.
x-elect can also be used for tasks outside the marriage sector. Unlike pick & place systems, there is no need for additional sorting or vibrating stations. The bolts can be removed from the original transport packaging, thus dispensing with the need for additional handling. The system supports the fast integration of new component variants, reduces the number of manual work steps, and prevents incorrect manual loading.
Since the compact system requires hardly any pneumatic assistance, its operation is mostly quiet and energy-efficient. It consists of only a few mechanical components and is therefore very easy to maintain.
The commissioning of the new Dürr system is simulated virtually. Users can therefore optimize their station layout in advance, enabling them to save space as they integrate the design into existing systems. This ensures a smooth integration. Industry 4.0-compliant interfaces for peripheral systems and data utilization add value for the customer.
Customer benefits at a glance:
- Highest system availability through automation
- No incorrect loading of the bolt nests
- Bolts picked from the original container
- Compact dimensions
- Easy to maintain, dirt-resistant, few mechanical components
- High flexibility of bolt applications possible
- Easy integration into existing bolting stations
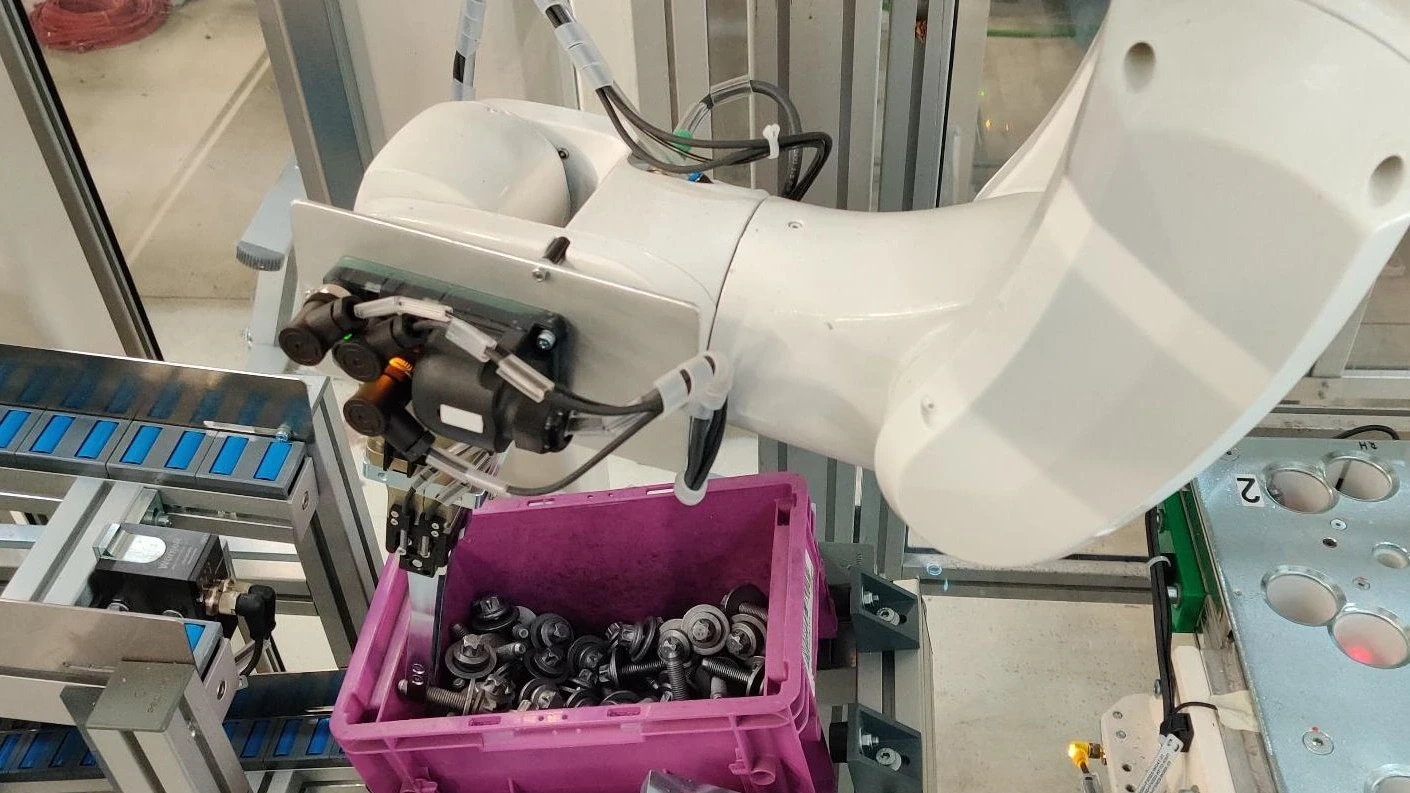
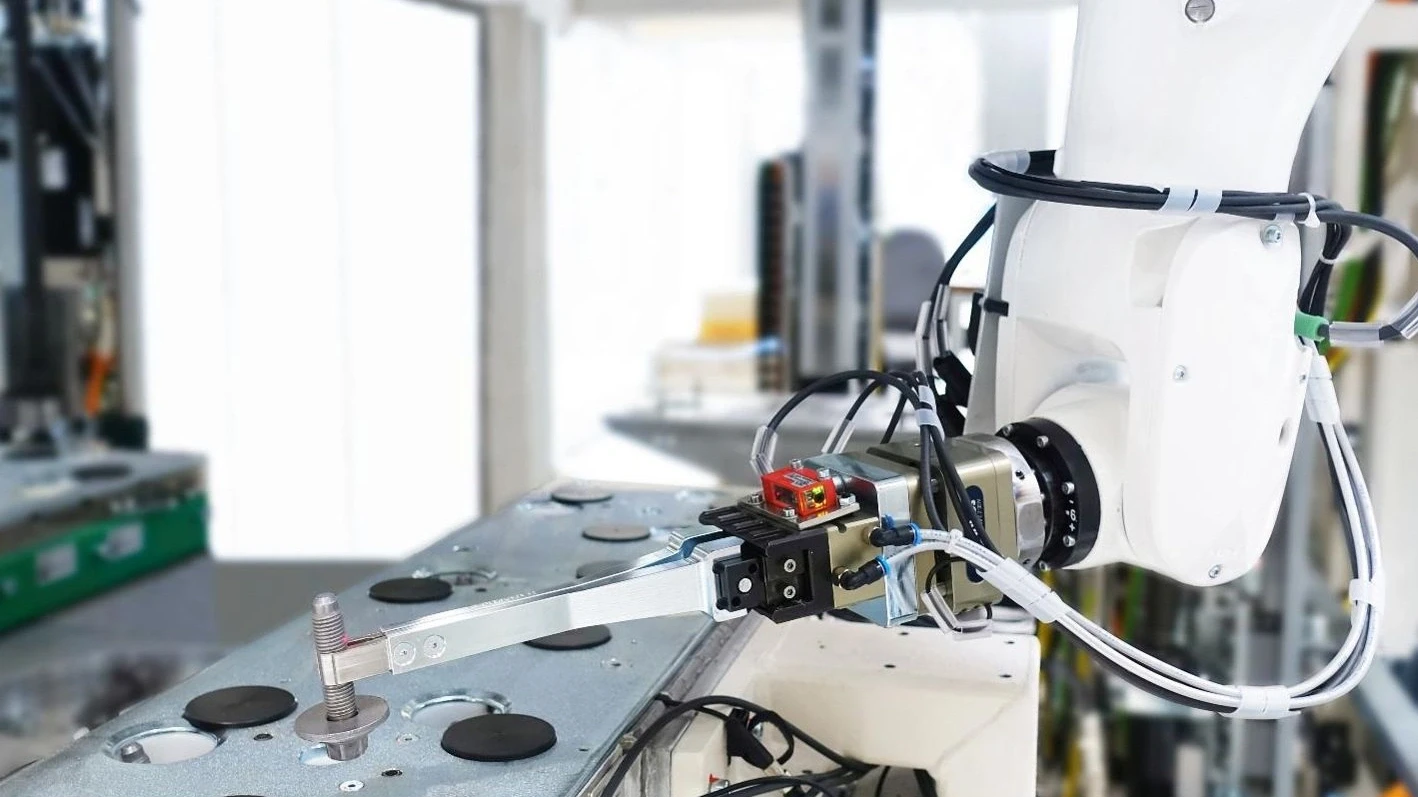